Pressure Leaf Filters
amafilter – LFC Lochem (Filtration Group Process Systems) designs, develops and manufactures advanced vertical and horizontal pressure leaf filters. A pressure leaf filter is a filter with a large specific filtration area due to the shape of the filter elements. A pressure leaf filter produces high filtrate clarity after the clarification run. All kinds of filter aids can be used in our pressure leaf filters.
Applications
Our innovative Vertical & Horizontal Pressure Leaf Filters are well known for e.g. Edible/vegetable Oils, Biofuel/diesel, Gelatin, Oleo chemical, Mining applications, metal plating bath filtering and Amine cleaning in the Oil & Gas market.
The pressure leaf filter is an enclosed filtration system and can be fully automated. This filter produces a high filtrate clarity after the clarification run and is also suitable for all kinds of filter aids. The regeneration time between the filtration cycles is short.

Vertical Pressure Leaf Filter (VPLF / Versis)
The pressure leaf filter is an enclosed filtration system and can be fully automated. This filter produces a high filtrate clarity after the clarification run and is also suitable for all kinds of filter aids. The regeneration time between the filtration cycles is short.
The pressure vessel is filled with solution. Each filter element is surrounded by solution. The solution is pressurized and the liquid is pushed through the filter cake and into the filter element.
The filtrate goes out of the filter through the filter outlet. The solid particles remain on the elements as a filter cake.
Make a precoat layer (optional) on the filter elements before starting a filtration cycle. Supply the solution (with added precoat aid) through the filter until the precoat layer has the correct thickness.
A filter cake is necessary to get a clear filtrate. The first filtrate will not be clear. Keep supplying solution to start building a filter cake. Filtration starts when the filter cake is of sufficient thickness and the filtrate becomes clear.
A filtration cycle ends when you get the:
– maximum permitted pressure difference
– maximum design pressure
– maximum cake thickness.
At the end of a filtration cycle the contents of the pressure vessel are removed. The cake is dried with air, an inert gas or steam. After the pressure is released the bottom valve is opened. The vibrators start and shake the cake loose from the filter elements. The cake goes through the bottom valve.
Vertical Pressure Leaf Filter advantages
- High filtrate clarity
- High yield low product losses
- Large filtration area – small footprint (high headroom)
- No filter cloth – no washing or cloth replacements
- Totally enclosed operation – no contact with air/moisture
- Positive pressure – no vacuum or lowered pressures necessary
- Wet or dry cake discharge
- Possible extraction of the filter cake within the filter
- Easy to automate – operation with minimum labour
- Fast and effective cleaning without manual interference.
- Mechanically simple
- Easy access to the filter leaves for maintenance or extra leaf cleaning
- Intensive cleaning of filter medium is possible
- Improved housekeeping
- Steam heating optional
Typical applications Vertical Pressure Leaf Filter
Dry cake discharge
– Edible oils
– Crude oil
– Bleaching
– Winterisation
– Sulphur
Wet cake discharge
– Sugars
– Water glass
– Beer
– Brine
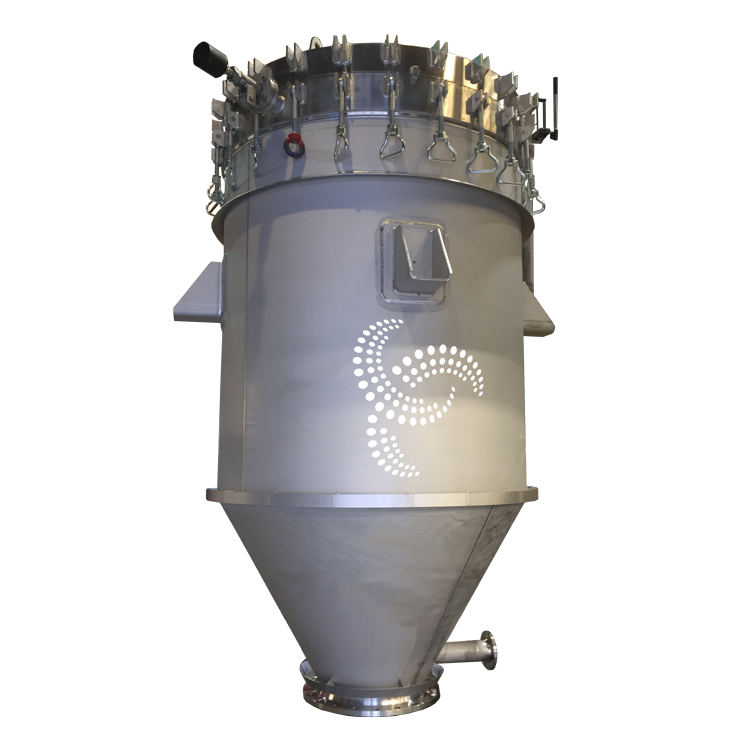
Horizontal Pressure Leaf Filter (HPLF)
The horizontal pressure leaf filter is an enclosed filtration system and can be fully automated. This filter produces a high filtrate clarity after the clarification run and is also suitable for all kinds of filter aids.
Key characteristics (sulphur filtration)
– Big filtration surface,
– Easy to clean filter plates,
– Heating jacket in order to prevent solidification
– The pressure leaf filter itself has no rotating parts, thus keeping maintenance to a minimum
These advantages result in an economical filtration solution. For cake discharge the carriage with the filter leaves is driven outside the tank with an electric or hydraulic system. With a Retractable Shell system, the filter leaves are exposed by moving the tank away from the bundle.
The bayonet ring is opened hydraulically. The cake discharge is easily done with the filter opened.
The Retractable bundle type filter is equipped with a self-sealing quick release manifold coupling which is steam heated.
The Horizontal Pressure Leaf Filter, which we supply in the filtration cycle of liquid sulphur, can be tailor made to fit your requirements, in any of the following setups:
Retractable bundle (RB)
The shell doesn’t move; the bundle with filter elements moves in and out of the shell.

Retractable shell with an overhead suspension frame
The bundle doesn’t move, the shell hangs from a support structure and moves over the bundle.
Retractable shell with a lower support frame
The bundle doesn’t move here either, the shell is supported by rails and moves over the bundle.

Filter elements
The leaf spacing is 125 mm to allow for precoat and longer filtration times. The filter leaves are mounted on a manifold which allows for easy removal and mounting of the filter leaves.
Features and benefits
– Vertical position for easy cleaning
– Retanglar filter screens, double sided
– Five layers of wire mesh
– Reinforced binding around the full circumference of the filter leaf to protect the rim during manual cake removal by tapping
Please select our main website for further information